Future-proof logistics planning

Based on a brownfield layout, one of the most advanced automotive production facilities was built near Beijing, China. Following the approach outlined by Industrie 4.0, it was imperative to apply highest possible technological standards and the most innovative concepts. With the successful implementation of these standards, the plant is now considered to be a model factory in Asia. Based on the customer’s requirements, UNITY developed and implemented a state-of-the-art logistics concept on-site within 18 months. The project team consisted of both German and Chinese UNITY employees who were located in Germany and China for the entire duration of the project. This ensured that a local point of contact was always available to cater to the customer‘s needs and guarantee an efficient execution of the project. In addition to the process and layout planning, focus was also placed on planning of AGVs which ensure a highly automated supply of parts and components to the assembly line. The goal of achieving a paperless logistics system was enabled by utilizing other innovative technologies such as pick by voice, pick by light and e-tags.
From conception to implementation in less than 1.5 years
Automated supply of 90 % of all assembly line components
Future-proof planning of all logistics areas in the >150,000 sqm assembly facility
Your Contact
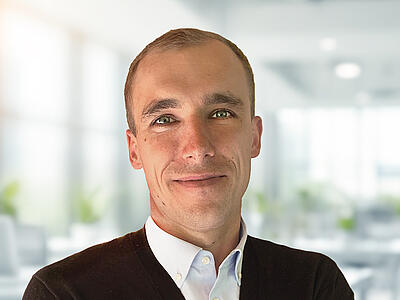
Manuel Kumle
Business Area Lead
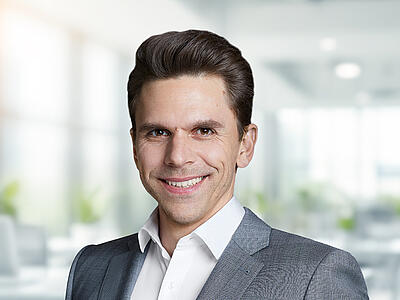
Ingo Neumann
中国区董事总经理