Increasing efficiency and lead times
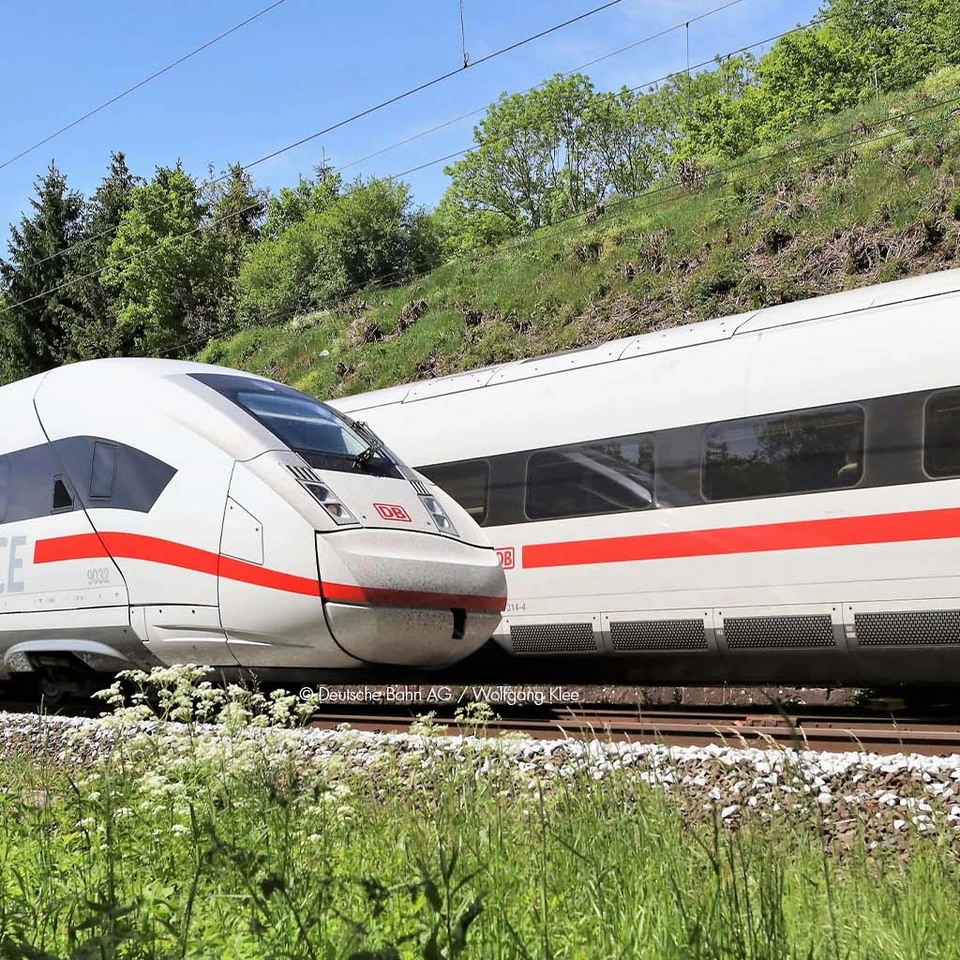
End-to-End Process Optimization for the DB FZI Wheelset Workshop in Kassel
Deutsche Bahn trains cover thousands of kilometers every year and therefore, the wheelsets have to be serviced regularly. At DB FZI, this is done at its wheelset workshop in Kassel. Deutsche Bahn called upon UNITY‘s expertise to conduct a potential analysis for increasing productivity and reducing costs. Together, it was possible to identify levers for increasing efficiency and lead times. This was based on an analysis of the production data from the past twelve months, the recordings of maintenance processes, and the bottlenecks that were identified in the production system. More than 100 improvement potentials were uncovered, monetarily assessed and finally, the top 30 technology potentials for the automation of wheelset production were identified and prioritized. In parallel, a dynamic simulation model was built to identify changing bottlenecks depending on the combination of quantity and maintenance tasks. Results from the simulation clearly showed that the order sequence alone has a strong influence on the production key figures. Consequently, efficiency cannot be increased solely through automation measures. Rather, it must be increased through the appropriate optimization of planning and control above all else. Thus, possible application scenarios of modern MES (Manufacturing Execution Systems) were discussed and assessed in economic terms. Relevant potentials also exist in the areas of organization and management structures. All of the findings were prioritized and visualized in a holistic roadmap. In particular, the wheelset workshop benefited from the fact that UNITY considered the entire system from the very beginning and brought together all of the relevant stakeholders. This made it possible to determine target-oriented measures for the DB plant in Kassel.
Technologies analyzed: 30
Potential for reduced processing time: -30%
Potential for increased inventory: +25%
“UNITY has enabled us to decide exactly which concrete steps are required to further develop our wheelset production through its in-depth technology know-how and by taking an end-to-end approach, involving all knowledge carriers, and mapping complex maintenance processes in the material flow simulation.”

Falk Pohl
Head of Strategic Product Management
Your Contact
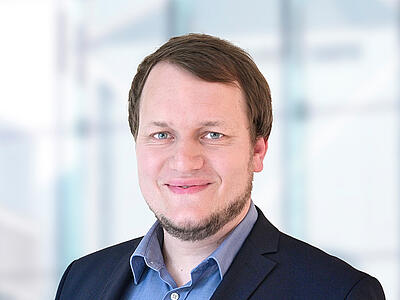
Thorben Kerkenberg
Head of Smart Factory & Operational Excellence