Process analysis for an integrated view of the DMU equipment process
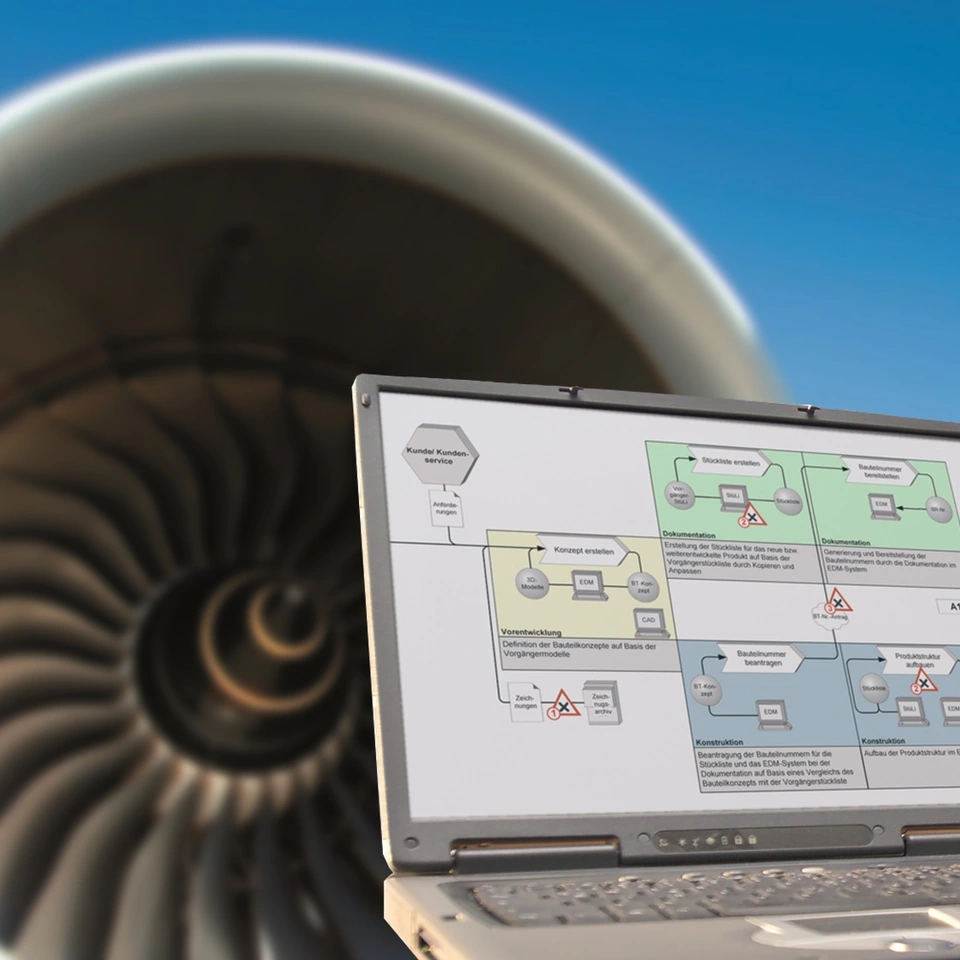
Reduced Development Time through Consequential Process Management
Whether involved in planning, construction or manufacturing, UNITY has been involved in shortening development times for the largest passenger aircraft ever built, the Airbus A380, and reducing costs for Airbus for three years now. An example of a complex challenge that arose during the development of the A380 program is the equipping of each aircraft with electrical and non-flightrelevant devices. Depending on which airline is buying the airplane, the equipment requirements are different. Until shortly before the airplane is delivered, the customer still has the opportunity to customize how the equipment is configured according to his own requirements. For example, the interior equipment, air conditioning system and media technology system can all be customized.
To save time and money, computer-aided analysis (a "digital mock up” - DMU) is carried out before the equipment is actually installed. Suppliers to Airbus deliver CAD model data for every piece of equipment, and this can be checked and integrated into the digital reproduction of each A380. This requires high quality data and must be carried out at the right time. We found that this is precisely where the original DMU equipment process exhibited potential for improvement. Alongside the appropriate IT tools, the DMU equipment process is dependent above all on solutions in the areas of process and data management, as well as in the area of supplier integration. UNITY was assigned with optimizing these processes.
UNITY first conducted a process analysis that looked at the entire DMU equipment process as a whole. This step created additional transparency, bringing to light information about individual processes, resources, responsibilities and information flows for data suppliers and data users. From this analysis possibilities for improving organizational and IT-related aspects of the DMU equipment process became apparent. These were then prioritized and time-phased within the context of an overall implementation strategy.
For Airbus, the optimized DMU equipment process has tangible benefits: Lead times have been reduced, rectification costs have sunk and the degree of product maturity is now higher at an earlier stage.
Reduced Development Time
Reduced rework costs
Product maturity increased at an early stage
“With their methodical way of proceeding and their high degree of competence in terms of processes and technology, UNITY helped put us in the position to initiate a comprehensive improvement program for the DMU equipment process for the A380. With this program we were able to significantly shorten the lead time required for the integration of the equipment.”

Klaus Schwietzer
Development Manager A380 Germany
Your Contact
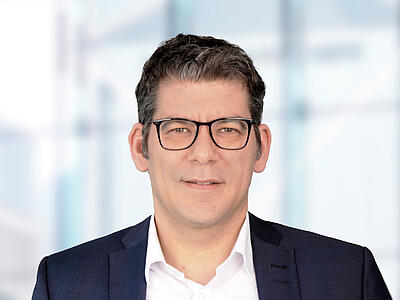
Michael Wolf
Partner, Business Area Lead